In the evolving landscape of jewelry manufacturing, surface finishing is pivotal in balancing aesthetics with durability. Among emerging technologies, electrophoretic coating (E-coating) has become a cutting-edge solution for protecting delicate jewelry designs. This article explores the science, advantages, and applications of E-coating in jewelry production while contrasting it with traditional methods like enameling, PVD, and electroplating.
What is E-Coating on Jewelry?
E-coating (electrophoretic coating) is an eco-friendly method to protect jewelry with a durable, scratch-resistant layer. Using an electric current, charged particles in a water-based solution bond evenly to the metal surface. The piece is then baked to harden the coating, ensuring long-lasting shine and resistance to tarnish. Unlike traditional plating, which minimizes waste and avoids toxic chemicals, e-coating is eco-friendly, producing. It ensures consistent coverage, even on intricate designs, and resists tarnishing or corrosion over time. This process combines sustainability with long-lasting beauty, making it a go-to choice for modern, high-quality jewelry that prioritizes both style and environmental responsibility.
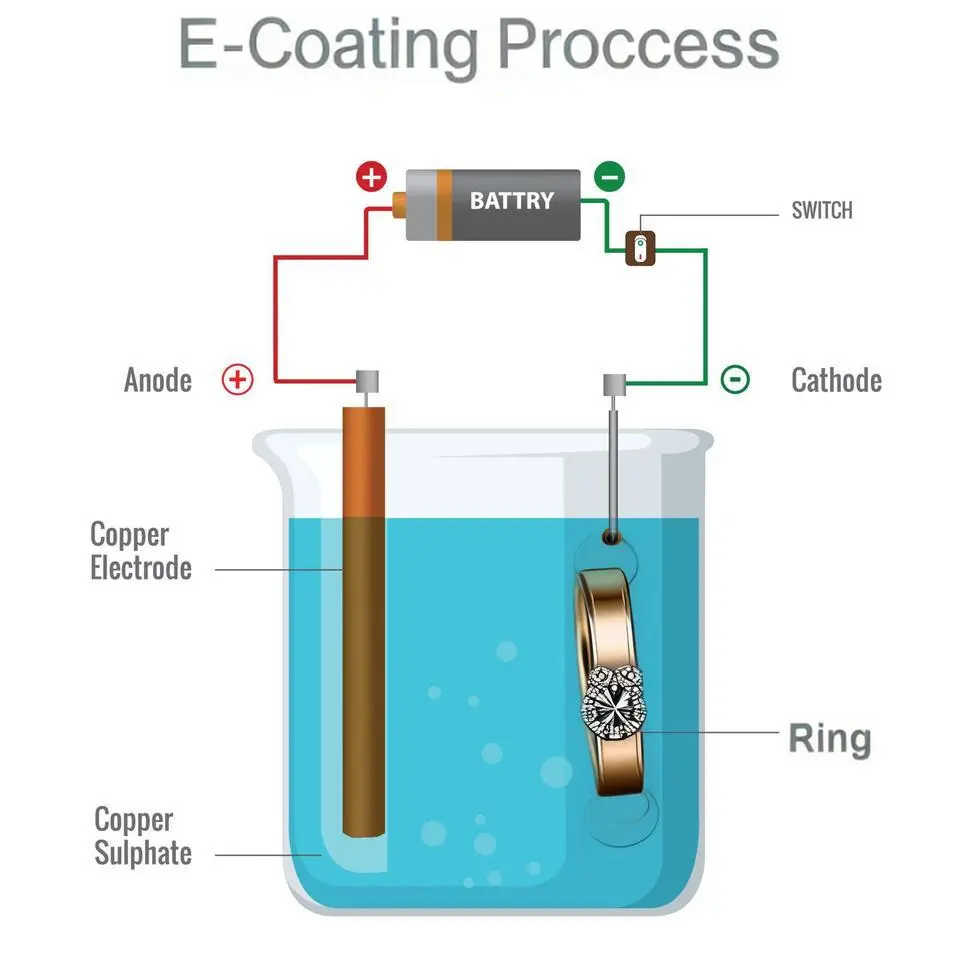
E-Coating Process
Generally, the e-coating process involves three key processes critical for achieving a durable, scratch-resistant finish with uniform coverage, ensuring the jewelry’s surface is both resilient and aesthetically flawless.
Surface Preparation
Surface prep for e-coating starts with ultrasonic cleaning to strip oils and residues, ensuring perfect adhesion. Polishing creates a flawless surface, and final rinses eliminate residue, leaving a pristine base for even, long-lasting coating, ensuring the coating clings perfectly.
Electrophoretic Deposition
The jewelry is submerged in a water-based solution containing charged particles of the coating material (e.g., epoxy or acrylic). An electric current is applied, attracting particles to coat the entire surface evenly. This electric fusion ensures no pooling, just a smooth, consistent layer.
Curing
After coating, the piece is oven-cured with controlled temperatures at 160°C, transforming the liquid layer into a smooth, scratch-resistant finish. This curing ensures the finish won’t crack or peel, enduring daily use with ease.
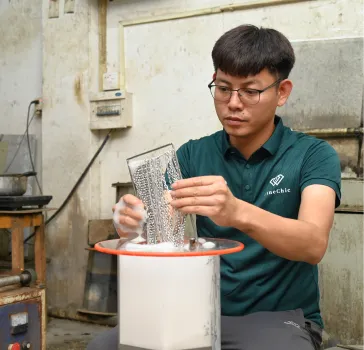
Advantages of E-Coating for Jewelry
As consumers prioritize sustainability and quality, e-coating bridges the gap between eco-conscious practices and luxury aesthetics. Discover the transformative advantages of e-coating, offering jewelry robust protection, seamless coverage, eco-friendly practices, and smart cost savings.
Enhanced Durability
E-coating creates a resilient barrier against scratches, corrosion, and daily wear, preserving jewelry’s original luster and integrity. Ideal for everyday pieces, it ensures long-lasting beauty and protection.
Comprehensive Coverage for Intricate Designs
The submersion process guarantees uniform protection, even in complex shapes and hard-to-reach areas. This enhances overall durability, ensuring every detail is strengthened and preserved for a flawless finish.
Eco-Friendly & Sustainable Practice
Using a water-based process, e-coating minimizes toxic waste, aligning with eco-conscious trends. It meets the demand for sustainable jewelry solutions, respects the environment, and promotes green practices.
Cost-Effective Long-Term Solution
E-coating reduces maintenance costs and the need for frequent reapplication. Offering superior durability compared to traditional plating, it’s a smart investment for jewelry that lasts, providing long-term value and peace of mind.
Things to Consider Before You E-Coat Your Jewelry
When evaluating e-coating for jewelry, it is essential to consider several key factors to guide your decision-making. While this process enhances durability and extends the lifespan of pieces, it is important to note that it is not a universal solution. Please find below a detailed list of the most important factors to consider.
Metal Compatibility
E-coating excels on gold, silver, and brass due to their seamless bond with nano-ceramic. However, costume jewelry metals may warp or discolor, while hard metals like titanium resist adhesion. Stainless steel and tungsten require specialized polishing, increasing costs. Alternative finishes like PVD may suit such metals better.
Design Intricacies
E-coating’s uniform layer can challenge fragile jewelry elements. Heat-sensitive materials like plastic or enamel risk damage, while intricate designs may trap air bubbles, causing texture issues. A solution is a post-coating assembly, adding decorative elements after e-coating to protect their integrity.
Color & Finish
E-coating has been found to result in a color change, with metals such as silver acquiring a muted, slightly darker hue post-coating and gold appearing more saturated. Due to the coating’s unique property, matte surfaces will develop a subtle sheen, as the coating adds a slight luster. In addition, you should carefully consider the choice of coating colors. It is essential to plan thoroughly before application, as the removal process is complicated and can result in damage to the metal.
Cost Economics
The cost of e-coating is dependent on several factors, including the complexity of the design, the type of metal being coated, and the required level of polishing. Simple pieces generally incur less expense, while intricate designs require a greater investment in labor. A thorough pre-treatment process is paramount to ensure the absence of flaws beneath the coating.
How Long Does E-Coating Last?
Unprotected jewelry, such as gold and silver plating, is exposed to fading, oxidation, and scratches, especially from sweat, perfume, and detergents, within 6 months to 2 years. E-Coating provides a denser protective layer, which can extend the wear time to 2-5 years while improving resistance to sweat, friction,n, and minor scratches. This makes it an ideal solution for frequently worn jewelry.
E-Coating, Enameling, PVD, and Plating: What Are the Differences?
In short, the plating lasts for a relatively short period, while e-coating can extend the life of jewelry to 2-5 years. PVD is typically employed for stainless steel jewelry, while enamel is well-suited for jewelry with intricate coloration.
E-coating | Enameling | PVD | Plating | |
Feature of Process | Electric field drives deposition of resin/paint | High-temperature melting and solidification of glass glaze | Atomic/molecular deposition under vacuum | Electrolytic reaction Metal ion deposition |
Process Temperature | 160-200°C Medium temperature curing | 750-850°C High-temperature sintering | 50-500°C (range tolerated by the base material) | Room temperature to 80°C (solution temperature) |
Coverage Uniformity | Full coverage of complex structures (including micropores) | Best on flat/regular surfaces | Deposition at eye level requires a rotating fixture | “Edge build-up” is likely to occur in recesses |
Color Diversity | Transparent/color optional (UV curing required) | Glaze color fixed (red/blue/green, etc.) | Metallic color + gradient effect (e.g. rose gold) | Metallic primary colors |
Eco-Friendliness | High | Moderate | Moderate | Low (Wastewater containing cyanides requires professional treatment) |
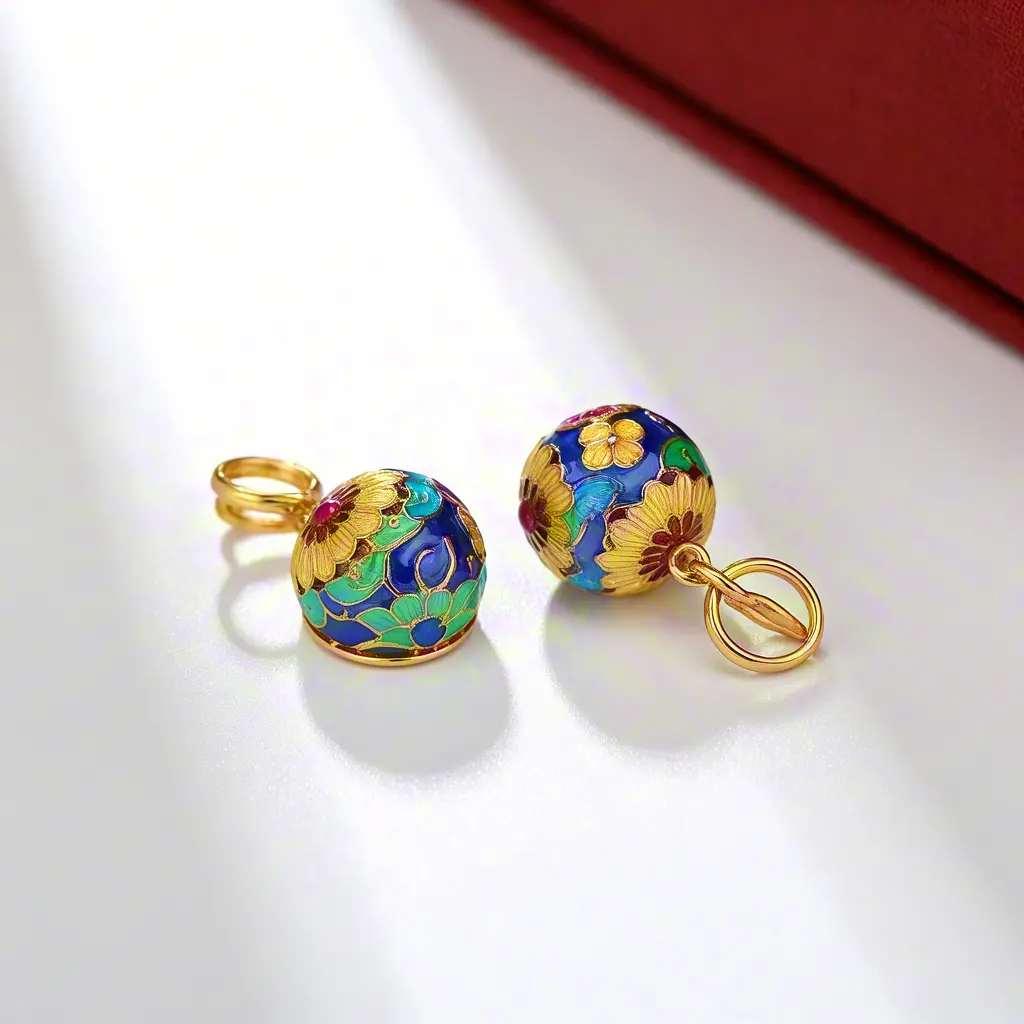
The Takeaway
E-coating represents the future of jewelry finishing, offering a blend of resilience, beauty, and environmental stewardship. Whether you’re designing a timeless engagement ring or a modern statement piece, this process ensures your jewelry withstands the test of time while aligning with global sustainability goals. In other words, to better fulfill your desires, you must contact a sustainable jewelry manufacturer who is familiar with the technique of e-coating jewelry.